Аппараты плазменной резки металлов серии "стандарт" типа «PLASMA S 105 / 156 / 188» в большинстве случаев являются идеальным оборудованием для резки металлов, будь то использование в небольшой металлобрабатывающей мастерской, в сервисных центрах и ремонтных цехах заводов по обслуживанию различного оборудования, машин и механизмов или на малых и средних промышленных предприятиях.
Преимущество данных аппаратов:
--------------------
• оптимальная цена;
• высокое качество продукции;
• продуманная эргономичная конструкция;
• удобное и легкое управление с системой индикации рабочего процесса;
• низкое и эффективное энергопотребление;
• более высокая стойкость сменных и расходуемых деталей;
• надёжная система защиты оператора и безопасной эксплуатации аппаратуры.
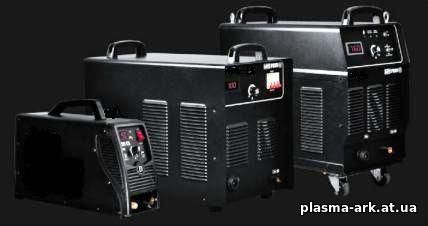
Предлагаемые модели аппаратов плазменной резки способны удовлетворить потребности большинства малых и средних предприятий, в производственном цикле которых присутствует такая операция, как резка металла.
Для авторемонтных мастерских, где требуется разрезать тонкие листы стали и алюминия, для небольшого судостроительно-судоремонтного или среднего машиностроительного завода, ремонтных цехов больших предприятий - отличным выбором станет аппаратура серии "стандарт" типа «PLASMA S 105 / 156 / 188», позволяющая резать в ручном и/или механизированном режиме металлы толщиной от 1 мм до 60 мм.
Эти новые трехфазные источники питания, благодаря хорошей мощности (рабочий ток 105A, 150А при ПВ=60% и 180А при ПВ=50%), а также использованию новых плазмотронов типа OL-100/130, OL-150/170 и OL-170/190 для соответствующих аппаратов (см. Раздел «Резка. Плазмотроны. Часть 1.»), предназначены резать металлы малых и средних толщин (максимальная толщина резки равна 35 мм, 50 мм и 60 мм соответственно).
Высокие показатели непрерывного цикла (ПВ=100% при t=400С на рабочих токах 90А, 130А и 165А данных аппаратов) и оптимальная скорость резки делают, их хорошим оборудованием для механизированной (автоматической) резки металлов на различных производствах - рекомендуемая толщина для высококачественной по ДСТУ EN ISO 9013:2019 (ISO 9013:2017) резки и хорошей производительности равна 20 мм, 30 мм и 35 мм соответственно для "PLASMA S 105 / 156 / 188".
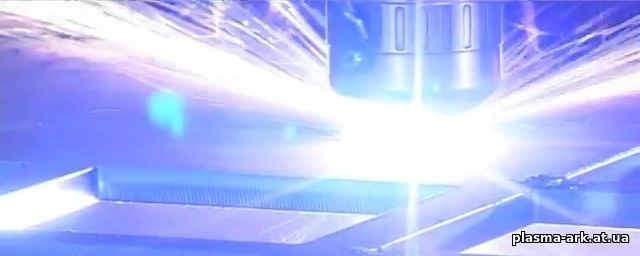
Источники питания данных аппаратов совместно с вышеуказанными плазмотронами предназначены для высокопроизводительной и качественной механизированной резки металлов малых и средних толщин и/или ручной разделительной резки.
Схема источников питания построена на инновационном трёхфазном инверторном преобразователе, созданном на основе современных IGBT-технологий, с высокочастотным возбуждением пилотной (дежурной) дуги и крутопадающей выходной характеристикой, имеют плавную регулировку выходного рабочего тока с постепенным автоматическим наращиванием до установленного значения. Благодаря использованию мощных энергоэффективных транзисторов IGBT и применению принципа широтно-импульсной модуляции (PWM), выпрямленное напряжение сети преобразуется в высокочастотное переменное напряжение (100 кГц), которое подается на первичную обмотку силового трансформатора на ферритовом магнитопроводе. Затем, на вторичной обмотке получается переменное высокочастотное напряжение, которое затем преобразуется в постоянное. Такой принцип работы позволяет использовать силовой трансформатор значительно меньшего размера и уменьшить вес оборудования, а также ведет к увеличению КПД аппарата до 87...93%.
Система обратных связей обеспечивает отличную стабилизацию установленного оператором тока резки в рабочем диапазоне напряжения на дуге, применяемые системы термозащиты, защиты от перепадов напряжения питающей сети, «мягкого» поджига дежурной (пилотной) и основной дуги, подачи сжатого воздуха (рабочего газа) для соответствующих режимов работы. Одновременно с оригинальными плазмотронами для ручной или механизированной резки типа OL-ххх/ххх, аппараты обеспечивают качественную резку всех токопроводящих материалов (сталь, н/ж сталь, алюминий, титан, медь, чугун и др.), возможность резки решёток с автоматическим включением пилотной дуги, а также работу при изменении напряжения питающей электросети + /-15% от базового значения 380 В.
Ручная резка: Iр=25А, Сталь - S=2мм.
Оптимальную работоспособность плазмотрона (резака) обеспечивает надёжная микропроцессорная система управления и контроля источника питания. Плазмотрон также оборудован системой защиты оператора от поражения электрическим током.
Цикл резки: «продувка» плазмотрона в начале и в конце резки, «мягкого» поджига дежурной и основной дуги, контроль тока и напряжения, подачи сжатого воздуха, система стабилизации выходной мощности и пр., управляется специальным микропроцессорным модулем с системой диагностики.
Применение высококачественных плазмотронов типа «OL-ххх/ххх» (см. Раздел: «Резка. Плазмотроны. Часть 1.»), в комплекте с устройством автоматического поддержания зазора между соплом плазмотрона и листом разрезаемого металла машины с ЧПУ или РТК, обеспечивает хорошую производительность, минимальную ширину и высокое качество кромок реза (согласно ДСТУ EN ISO 9013:2019 (ISO 9013:2017)) на рекомендуемых толщинах металла (см. Таблицу).
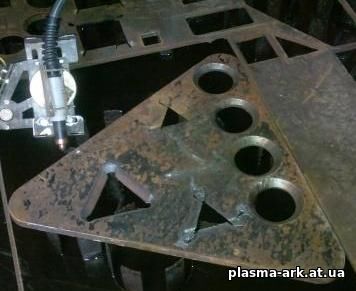
Особенностью данных аппаратов является:
-----------------------
- Непрерывный контроль напряжения питающей сети, проверка наличия неисправностей и приведение источника питания, при необходимости в безопасное состояние.
- Автоматическая система проверки наличия всех фаз питающей электросети (как при запуске, так и во время работы), во избежание не надлежащей работы установки при случайном отключении одной из фаз.
- Функция "продувки", которая позволяет устранить накопившийся конденсат до процесса резки и обеспечивает охлаждение резака после выключения дуги, что способствует снижению нагрева деталей плазмотрона и позволяет увеличить срок службы расходных элементов.
- Высокая электромагнитная защищённость в соответствии со стандартом ДСТУ EN 60974-10:2018, что позволяет использовать аппараты в непосредственной близости от различного электронного оборудования (как, например: компьютеры, системы ЧПУ и т.д.).
- ВЧ-поджиг дуги с высоким напряжением (осцилятор), которое гарантирует надёжное зажигание дежурной дуги и позволяет работать на металлах с лакокрасочным или другим покрытием.
- Взрывозащищенное исполнение системы воздушной магистрали.
- Режим работы «строжка», который выбирается на панели управления.
- Дисплей на котором указывается ток резки и соответствующий ему диаметр сопла.
- Разъем RS232 для обновления и/или настройки программного обеспечения.
- Более высокий ресурс работы сопел и электродов плазмотрона.
- Центральный разъем подключения резака с системой защиты от случайного соприкосновения с токоведущими частями и поражения электрическим током.
- Инверторная технология источника питания, рабочая частота 100кГц.
- Поставляются в комплекте с плазмотронами типа OL-ххх/ххх и необходимой длиной коммуникаций (см. Раздел: «Резка. Плазмотроны. Часть 1.»).
- Источники питания соответствуют стандарту ДСТУ EN 61000-3-12:2017.
- Источники питания соответствуют директивам ЕС: LVD 2014/35/EU, EMC 2014/30/EU, RoHS 2011/65/EU.
Многолетний опыт в области плазменных технологий, профессионализм и теоретическая подготовка в области моделирования сложного оборудования – вылились в оптимальные аппараты для плазменной резки металлов, в т.ч. в механизированном (автоматическом) режиме.
Они являются полнокомплектными установками для качественной плазменной резки в среде сжатого воздуха (плазмообразующего / защитного газа) всех металлических материалов. Состоят из очень надёжных источников питания с электронным управлением, а также соответствующих им плазмотронов для получения хорошего реза на толщинах от 1 мм до 30 мм, 40 мм и 45 мм соответственно для "PLASMA S 105 / 156 / 188".
Максимальная толщина пробивки листа металла составляет:
--------------------
- при неподвижном плазмотроне 10 мм, 13 мм и 15 мм соответственно для "PLASMA S 105 / 156 / 188";
- при движении плазмотрона 20 мм, 30 мм и 35 мм соответственно для "PLASMA S 105 / 156 / 188".
Такие результаты стали возможны благодаря оптимальной конфигурации аппаратуры.
Для надлежащей работы оборудования с системами ЧПУ и/или РТК, аппараты снабжены аналоговыми / цифровыми интерфейсами, способными обеспечить качественное соединение.
При разработке этих установок, были учтены все необходимые требования, для получения стабильной и высокоэффективной плазменной дуги, позволяющей получать наилучшее качество реза, как с края листа, так и при пробивке, в т.ч. при резке тонких материалов.
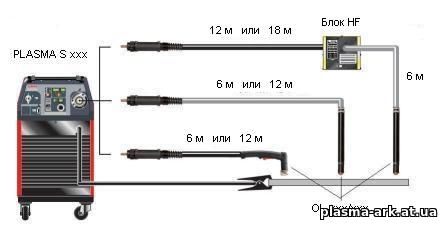
Особое внимание при производстве оборудования было уделено получению минимальных рабочих затрат при резке, тем самым обеспечивая существенное сокращение потребления электроэнергии, сменных и расходуемых деталей по сравнению с конкурирующими установками.
Панель управления аппаратов снабжена газовой консолью (регулятор с манометром и системой клапанов), позволяет выбрать и установить соответствующие параметры - "продувка" до и после процесса резки, рабочий расход плазмообразующего газа, а также служит для регулировки подачи сжатого воздуха.
Источники питания снабжены функцией рестарта пилотной дуги, которая автоматически прерывает и поджигает основную дугу, т.е. можно выбирать условия работы, например: для резки сеток и решеток.
Установки снабжаются различными наборами расходных материалов, в соответствии с выбранными рабочими параметрами, с целью получения хорошего качества реза и высокой производительности при минимальных эксплуатационных затратах.
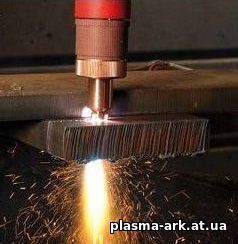
Техника резки (при ручном процессе) предельно проста – перемещение плазмотрона на упорах (или специальным соплом) по разрезаемому изделию. Удобный и лёгкий резак позволяет делать фигурные резы, резы по шаблону (копиру) и с циркульным устройством, осуществлять резку в труднодоступных местах.
Ручная резка: Iр=34А, Сталь - S=12мм.
Конструктивные особенности и технология производства плазмотрона позволяет быстро заменить расходные элементы для соответствия при резке разных металлов и в зависимости от толщины разрезаемого изделия, а также в случаях выработки их рабочего ресурса.
ОСНОВНЫЕ ТЕХНИЧЕСКИЕ ДАННЫЕ.
1.1. Аппараты типа «PLASMA S 105 / 156 / 188» предназначены для высокопроизводительной и качественной механизированной (автоматической) плазменной резки чёрных, цветных металлов и их сплавов толщиной до 20 / 30 / 35 мм по ДСТУ EN 9013:2019 (ISO 9013:2017), рекомендуемая до 30 / 40/ 45 мм и максимальная до 35 / 50 / 60 мм (соответственно аппаратам), а также ручной (полуавтоматической) разделительной резки металлов предельной толщиной до 45 / 60 / 70 мм.
1.2. В качестве рабочего и/или защитного газа используется сжатый воздух по ISO 8573-1:2010 [1:2:2], подачу обеспечивает специальный компрессор с системой подготовки воздуха. (Возможно применение в виде рабочего газа - азота или кислорода.)
1.3. Аппараты подключаются к электрической сети переменного тока номинальным напряжением 380В, частотой 50Гц. Качество электроэнергии по ДСТУ IEC 50160:2010.
1.4. Для охлаждения плазмотронов OL-100/130, OL-150/170 и OL-170/190 применяется рабочий газ (см. п.1.2.).
1.5. Аппараты изготавливаются в исполнении О5 по ГОСТ 15543.1-89.
1.6. Аппараты предназначены для работы в следующих условиях:
-- температура окружающей среды -100С...+450С и относительной влажности до 70% при температуре +270С;
-- высота над уровнем моря, не более, 1000 м.
1.7. Аппараты (кроме плазмотронов) по способу защиты от поражения электрическим током соответствует ДСТУ EN 60974-1:2014.
1.8. Степень защиты источников питания IР43S по ДСТУ IEC 60529:2019.
1.9. Аппараты соответствуют ДСТУ EN 61000-3-12:2017.
ТЕХНИЧЕСКИЕ ХАРАКТЕРИСТИКИ ИСТОЧНИКОВ ПИТАНИЯ.
Наименование |
PLASMA S 105 L |
PLASMA S 156 L |
PLASMA S 188 S-L |
Напряжение питающей
сети, 3ф., 50/60 Гц, В
(+/-15%) |
380 |
380 |
380 |
Максимальная
потребляемая
мощность, кВА |
16,6 |
27 |
34 |
КПД, % |
85 |
85 |
85 |
Напряжение Х.Х., В |
270 |
290 |
300 |
Рабочее напряжение, В |
80…165 |
80…180 |
80…200 |
Рабочий ток, А
ПВ%,
(при t=400С, 10 мин.,
ДСТУ EN 60974-1:2014) |
20...105
105А – 60%
90А – 100% |
20...150
150А – 60%
130А – 100% |
20...180
180А – 50%
165A -100% |
Регулировка тока |
плавная |
плавная |
плавная |
Рекомендуемая *
толщина резки
металла, мм: сталь
медь
алюминий |
30 (20)
8
20 |
40 (30)
13
35 |
45 (35)
15
40 |
Максимальная
толщина разрезаемого
металла (сталь), мм: |
35 |
50 |
60 |
Предельная толщина
разрезаемого металла
(сталь), мм: |
45 |
60 |
70 |
Максимальная толщина
пробивки металла
(сталь), мм |
20 |
30 |
35 |
Габаритные размеры,
мм |
220х540х460 |
330х710х540 |
330х710х540 |
Вес, кг |
25 |
50 |
54 |
ПРИМЕЧАНИЕ:
--------------------
* - Рекомендуемая толщина резки металла - хороший рез и производительность в ручном (полуавтоматическом) или механизированном (автоматическом) режимах на максимальном рабочем токе.
В скобках - рекомендуемая толщина для высокопроизводительной и качественной резки металла (сталь) в механизированном (автоматическом) режиме на рабочем токе при ПВ=100%, качество - в соответствии с ДСТУ EN ISO 9013:2019 (ISO 9013:2017)).
Ориентировочная скорость резки металла (сталь) только для соответствующих вышеуказанным установкам плазмотронов OL-100/130, OL-150/170 и OL-170/190 приведена в Разделе: «Резка. Плазмотроны. Часть 1.».
П Р Е И М У Щ Е С Т В А предлагаемого оборудования и наших технологий:
-------------------------------------
-- новая надёжная электронная система управления аппаратуры плазменной резки: точная поддержка заданных параметров рабочего тока, стабилизация напряжения дуги, контроль всех параметров источника питания и плазмотрона, системы термозащиты, подачи и расхода сжатого воздуха, автоматический рестарт дежурной дуги, контроль входящих параметров питающей сети;
-- расширен диапазон стабильного горения дуги, что позволяет получать высококачественный раскрой металла (на рабочем токе при ПВ=100%) в механизированном (автоматическом) режиме толщиной от 1 мм до 20 / 30 / 35 мм, соответственно для "PLASMA S 105 / 156 / 188", согласно ДСТУ EN ISO 9013:2019 (ISO 9013:2017), диапазон 3...4;
-- плавное нарастание тока в начале резки позволяет начинать рез с пробивки листов стали толщиной до 10 / 13 / 15 мм при неподвижном или до 20 / 30 / 35 мм при движении плазмотрона, для соответствующих аппаратов;
-- новые оригинальные плазмотроны, обеспечивающие повышение проникающей способности плазменной струи в 2 раза;
-- повышение предела усталости поверхностного слоя металла свободных (не свариваемых) кромок не менее чем на треть, существенное снижение деформаций кромок реза;
-- снижает количество наплавленного металла при сварке, увеличивает её производительность и уменьшает уровень деформаций сварных соединений;
-- уменьшение зоны термического влияния дуги в 1,5 раза и микротвёрдости стали в среднем в 2 раза;
-- снижение насыщения кромок реза азотом;
-- отсутствие пор при последующей дуговой сварке по вырезанным кромкам;
-- минимальная деформация разрезаемых металлов, из-за высокой скорости резки обеспеченной повышенной мощностью плазменной дуги;
-- небольшие потери материала благодаря узкому резу (ширина реза на малых и средних токах резки практически равна диаметру канала сопла);
-- возможность резки загрязнённых, окрашенных, гальванизированных и оцинкованных металлов;
-- ПВ=100% на токах, обеспечивающих качественную механизированную резку металла соответствующих толщин;
-- правильная организация технологического процесса, соответствующая наладка оборудования, использование нашей аппаратуры и надлежащая квалификация резчика приводит, в ряде случаев, к выпуску готовых изделий, не требующих последующей обработки;
-- новая система возбуждения дежурной (пилотной) дуги сводит к минимуму уровень высокочастотных помех, что повышает надежность работы машин с ЧПУ и систем РТК;
-- специальная программа цикла начала процесса не допускает бросков тока, разрушающих сопло и электрод в момент возбуждения дуги и во время резки, что увеличивает стойкость данных деталей в среднем в 2 раза;
-- вся необходимая оператору информация о текущем режиме состояния аппаратуры отображается на передней панели аппаратуры;
-- повышенное рабочее напряжение дуги (в пределах ГОСТ 12.2.007.8-75), что обеспечивает стабильную плазменную дугу даже при изменении зазора «сопло – разрезаемое изделие» в пределах до 15 мм (в зависимости от типа аппарата и плазмотрона) на заданных толщинах;
-- плавная регулировка тока дуги (диапазон изменения 10…100% от предварительно заданного значения), что обеспечивает возможность подбора оптимальных технологических параметров резки;
-- циклограмма отключения силовых элементов при обрыве дуги и аварийных ситуациях исключает броски тока, что повышает надёжность источника питания, повышает срок службы сопел и электродов;
-- оптимальное воздушное охлаждение плазмотрона и воздушно-принудительное источника питания.
ПРИМЕЧАНИЕ:
--------------------
При изготовлении оборудования применяются высококачественные комплектующие производства Украины и ведущих зарубежных фирм, проходящие дополнительный входной контроль на нашем предприятии, что позволило достигнуть высокой надёжности аппаратуры. Все основные компоненты оборудования всегда находятся на нашем складе в г.Киеве, что обеспечивает быстрый замен, в случае их выхода из строя и/или ненадлежащей работы.
Наши специалисты проведут у Вас:
--------------------
-- наладку и запуск приобретаемой, а также восстановленной и/или модернизированной аппаратуры;
-- обучение обслуживающего персонала правилам безопасной и эффективной эксплуатации оборудования, технологическим
приёмам обработки металлов.
Наше предприятие:
--------------------
-- предоставляет полные гарантийные обязательства на поставляемое, восстановленное и/или модернизированное
оборудование сроком на 3 (три) года;
-- обеспечивает послегарантийное сервисное обслуживание;
-- осуществляет дополнительную поставку сменных, расходуемых и запасных частей.
Надеемся, что сотрудничество с нами поможет Вам в достижении намеченных целей.
Просим обращаться к нам по любым интересующим Вас вопросам.
Наши данные указаны в разделе «Контакты».
|